News
November 2015
Sculpture Corner
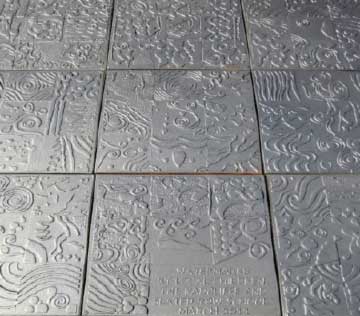
Watermarks
Castings designed by local children for the Milton Keynes Wolverton Mill Play Area. Part of a project under their direction, to complete a set of paving plates in cast iron.
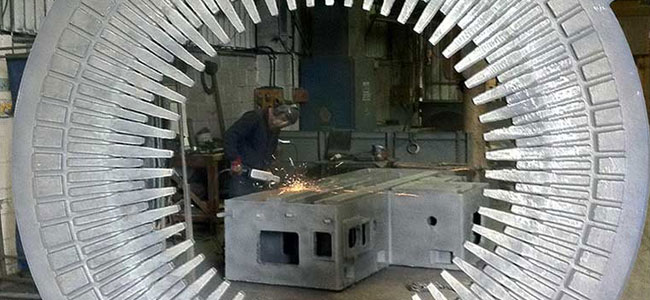
Non-Magnetic Stator End Plate
One of a pair of 4 tonne castings destined for a power station in Canada. The plates are used to start and finish the stator assembly. The plates are 2.7m diameter with 128 fingers to support the windings. The core is a 1200mm diameter shaft 40 foot long, which spins at such a speed it increases its diameter by 7mm. The Stator will produce 5.5 MW of electricity per hour. The assembly consists of layers of 5mm thick wafers of steel coated in resin, which is built up vertically on the first endplate. Each layer is built like brickwork, overlapping the sections below up to a height of approximately 10m. The area of work is strictly controlled to ensure no contaminants enter the assembly. After 3-4 month's work, the second endplate is placed on top and the two are tightened to compress the wafers and hold them in place. The square blocks around the outer diameter are more complex than can be seen on the photograph and are used to assist the movement of cooling air when the rotor is spinning.
Electric Furnaces
The photograph shows one of the electric furnace floors being hydraulically lifted from floor level to vertical to empty the molten metal into the awaiting ladle. Built on a platform the 850kg capacity furnace is like a hole in the ground. A ceramic crucible is wrapped with electric coils which are used to generate the energy required to melt the iron and raise the temperature to 1600°C . The coils themselves are water-cooled to stop them from melting. The whole floor tips to empty the metal when it is chemically correct and reached the right temperature.
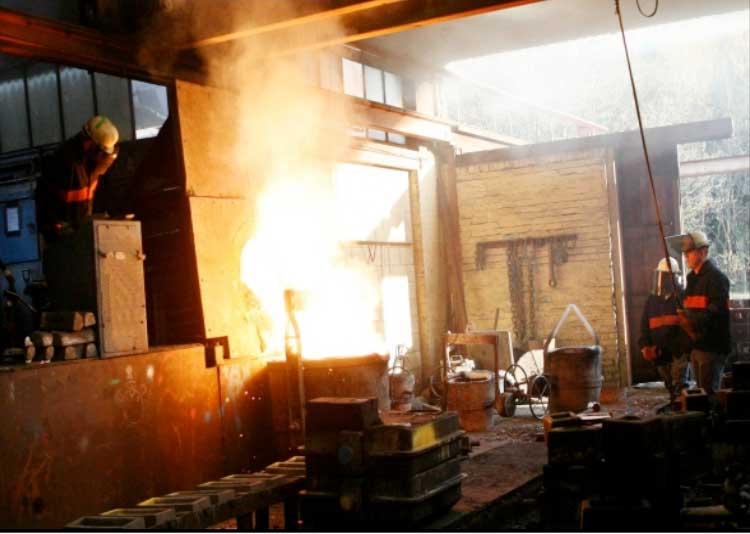
Material Certificates
More customers are asking for Material Certificates. The basis of these are the chemical analyses which we can produce from our own spectrograph. These analyses give precise percentages of the various elements which are present within the cast and we can check whether the element quantities are going to give the type of material required. The second test is on the mechanical values of the material, generally the tensile strength and the ductility but also the hardness values form part of the requirement. To calculate the tensile strength a machined, scaled-down sample of specific dimensions is placed within two jaws and stretched it until it breaks. This is then scaled-up and calculated to give the force required to break the test piece. Grade 17 iron describes an iron which has a tensile strength of equal to or just over 17 ton/in². In metric this is about 260N/mm² . These figures have always been the descriptive grades of iron. Imperial Grades 14, 17 and 20 (tons/in²) are common examples and their metric equivalents are rounded to the nearest 50 units Grades 200,250 and 300 (N/mm²) SG irons are made of two figures: e.g. SG 400/15. The first figure is the tensile (500 N/mm²) and the second figure 15 is the ductility, this a percentage and is based on the deformation which occurs before the item will break, its elasticity. The mechanical tests are conducted by outside independent laboratories who take several days to machine the test piece, test it and prepare the results. Occasionally the test piece has impurities or blow holes within its structure, these defects cause a loss in strength and are noted by the laboratory who examine the fractures on both sides of the break. This is why we always cast 2 test bars; the second is then sent for re-testing.