A Brief History
H.Downs and Sons was started on 1st April 1946 by Walter Downs and his father Horace. Read the full account of how this came about.
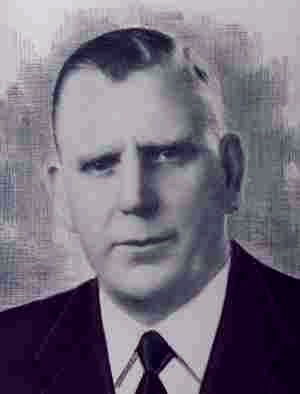
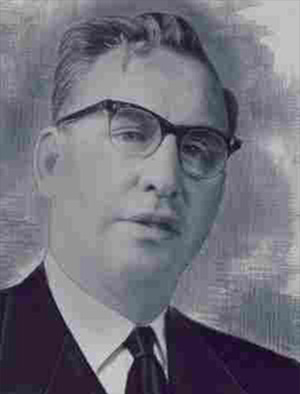
Peacock Works built, showing the original ground floor office reception and foundry behind.
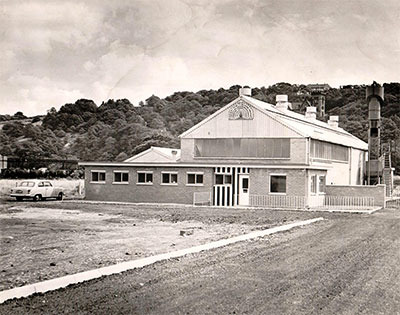
During the 1970's two of Walter's three sons Alan and Nigel, finished further education and entered the family business.
During the 1980's more technological developments were required for the future of the company, the limits to the maximum casting size was raised from 2 ton to 5 ton, procedures and documentation were introduced to benefit both customers and the foundry production.
Further advances in the acknowledgement of the benefits of SG iron prompted the brothers to contemplate installing electric furnaces along side the coke melting cupola. At this point John Booths of Ripponden was offered for sale offering the electric furnaces and other foundry production equipment, although dated the equipment could be used to produce special irons that were starting to come to the fore.
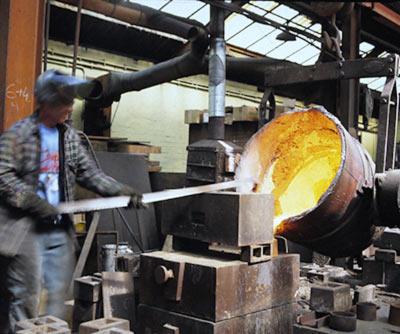
1986
In January 1986 H. Downs & Sons purchased John Booths. The two foundries together were capable of offering a wider range of iron alloys. The next few years saw an investment in both foundries to drag them out of the 1800's into modern production units.
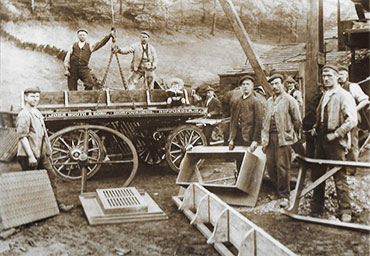
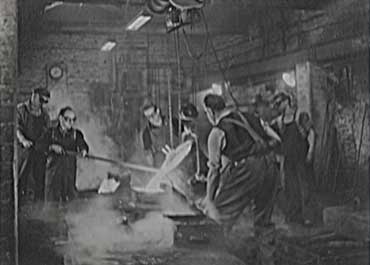
1993 saw the input of computers and a bespoke system designed by the brothers for the control of pattern equipment, production control and accounts.
1997
The late 90s brought about expenditure on environmental issues commencing with the purchase of a new cupola furnace for H. Downs in Huddersfield closely followed by a sand knockout and reclamation unit for John Booths.
A similar unit was installed in Huddersfield in 1998 allowing a change of moulding techniques and an increase in casting appearance. Finally, the furnace area was treated to a new roof to shelter the operatives.
The swelling at the top forms the water spray and collection area, it is accessed by a ladder on the left hand side. The furnace sways in the wind, but the climb to the top allows a good view up and down the valley.
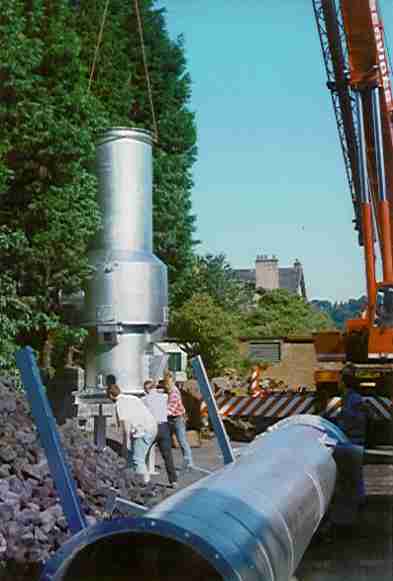
2005 H.Downs & Sons purchased the buildings next door. Formerly Pneumatic Conveyors Ltd. All production from John Booth was moved to the one 4 acre site. The original foundry was organised as the moulding, melting and casting area, the electric furnaces, moved from John Booths were installed to work in conjunction with the cupola to increase melting capacity for various alloys such as SG iron and Ni-Resist. The majority of employees from Ripponden made the move to Huddersfield.
Part of the new building, which was originally Pneumatic conveyors, was converted to a finishing department. A new shotblasting room was constructed and a smaller automatic unit was installed. Fettling takes place in this area and use is made of the existing paint spray booth. A pallet and shrink wrap area was created in dispatch.
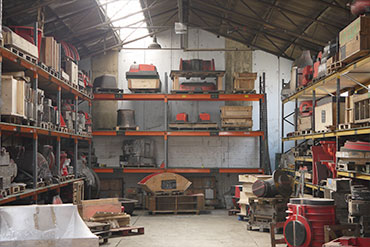
As a long-standing employer in West Yorkshire and experts in our field, we provide training for all aspects within the iron foundry. We have connections with Hudderfield University and provide apprenticeships for people interested in working in diverse roles across an exciting, creative manufacturing industry.
This website has been commissioned to celebrate H.Downs' 70th year of Manufacturing Excellence and broader contribution to Great British engineering. We hope it proves insightful to our customers and creates a point of reference for academic research.
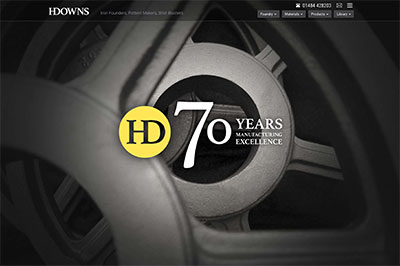
Contact us01484 428203