News
October 2010
Sculpture Corner
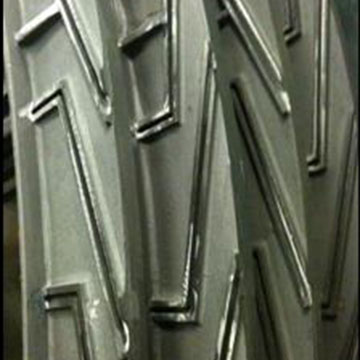
This time the sculpture comes from new/ old industrial castings. The photograph shows a close up of two half sets of a water wheel, left and right hand, 11 foot diameter. The slots cast into the sides are to hold buckets between the two wheels. They are being used in the reno- vation of an old mill in the Cotswolds.
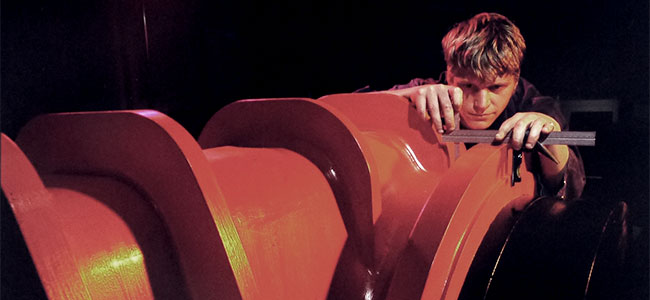
ISO 9001:2008 Certification
With our investment in bespoke computer equipment to control many aspects of our business, including administration, production, scheduling, material mixes and the analysis of metals, we were advised we were in a good position to gain accreditation to ISO 9001. We have, as a company, in the past, shied away from accreditation assuming it would involve a great deal of unnecessary paperwork. However, local grants gave us the opportunity to assess gaining accreditation was just a small step away and easily within our grasp. A MAS sponsored consultant came and visited and being very impressed with our present methods of production informed us it would be a very simple process to step up to meet the standard's requirements. We of course realised some customers would prefer us to have ISO9001 so we decided to go ahead for both our benefit and in order to meet our customers' requirements.
Apprenticeship Scheme
Half of H. Downs' workforce have been apprentices and, as the industry has shrunk, so have the educational establishments. We have, for the past 25 years trained in-house, on the job. We need to further this education to provide the industry with people with more knowledge. Our programme will pass on our experience of the foundry industry directly to our young trainees. We have voluntarily opted out of the local education system of NVQs etc. and will stand the cost of training ourselves without outside interference. This will allow us to give a more comprehensive education and understanding of the fundamentals of the entire process of production, from pattern making, through moulding techniques, the use of materials and the different characteristics of producing and casting various iron alloys. We will offer the course to other local foundries so they too can improve the quality of the workforce in this area.
Sand Mixer
This summer has seen an investment in another computer controlled sand mixer. The summer close down period allowed H. Downs to also replace a sand reclamation unit. This machine is 'self destructive' as it shakes and breaks down the used sand before pumping it back to the awaiting hoppers around the foundry for 90 % re-use.
R & D in Ni-Resist & SG
There are areas in the foundry industry, which have been around for thousands of years. Some materials have very expansive parameters of chemical analysis. One of these is Ni-Resist F1. The chemical analysis parameters would be set by producers of this material to give a hint of what is in the mixture without giving away the perfect composition. The material consists of austenite, a sticky soft base structure, interspersed with graphite clusters. On machining the clusters are plucked out of the austenite matrix giving a porous looking surface. H. Downs' aim was to experiment with the chemistry to improve the surface finish of this material. Various metallurgists were involved, but with no success from the various suggestions. Then we thought laterally and against advice managed to achieve a good surface finish through altering the structural composition of the iron. Further experiments are being taken to try and produce an as cast 'Low Temperature' SG iron. This material is eluding us so far and like most we have to resort to heat treatment to obtain the desired mechanical properties. However, the trials continue with various different mixes of different elements.