Moulding
Casting finish is aided by the use of furane sands and helps reclamation and recycling of sand. Our sand mixers are computer controlled, the chemical mixture of quantities take into account the temperature of the returned sand. Sand is mixed with a resin and time controlled on curing by percentage of acid catalyst additions.
Contact us01484 428203Moulding
Here shows a mould with both the top half and bottom half closed. The circular hole in the top right is where the metal will be poured in to the mould. The box on the left is without the top and shows the impressions in the sand made by the pattern. One of the patterns is on the box on the right. The metal will flow into the cavity, when cool we will have a solid casting.
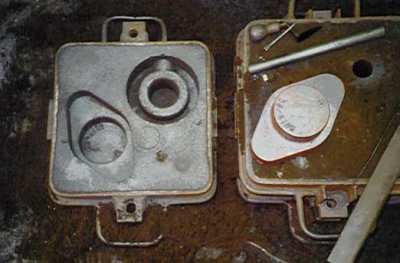
Small box moulding
Larger moulds are often made in the floor. The pattern is removed and the shape it has left in the sand is painted with a ceramic to smooth the sand surface. It also protects the sand to stop the heat of the metal from turning areas of the mould and the sand to a glassy material and sticking to the casting when the molten metal is poured in.
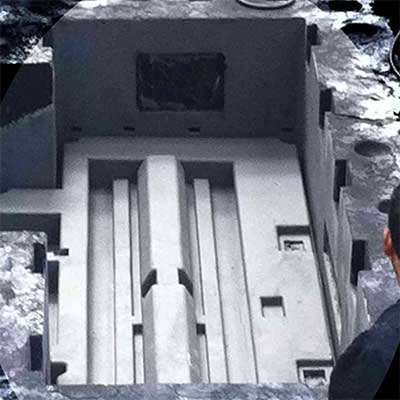
4200kg tool bed moulded in floor
A long mould formed in the foundry floor. It was originally designed as a fabricated beam to be welded. However, because it was so thin the steel was twisting under the heat of the welding. It is 5300 mm long. As iron cools the metal contracts, this causes the casting to bend and lift at the ends, so we shape it in the mould using camber to bend the mould so the casting will come straight when it cools.
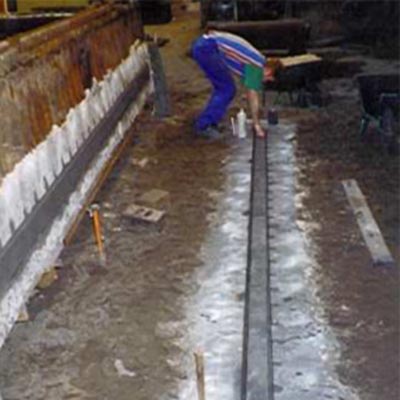
Long mould formed in the foundry floor
The person in the light shirt is stood in a mould for a stator made for GEC. The core to take out the centre of the casting is in the crane behind his head. The mould is contained in a metal box, the sand wall being about 75 mm thick. Pressures created when casting require a box to hold the sand in position.
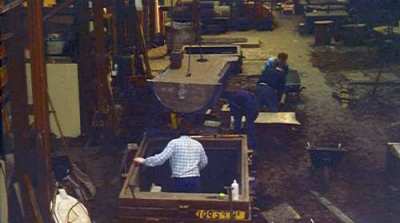
Core is lowered into the mould
The top half of the core is lowered into the mould and checked for being central. The cores and sides of the mould have been painted with coatings to give the castings a smooth surface when cast. There were 18 cores used to take out the centre and provide various access points for the electrics and panels to be fitted to the finished casting.
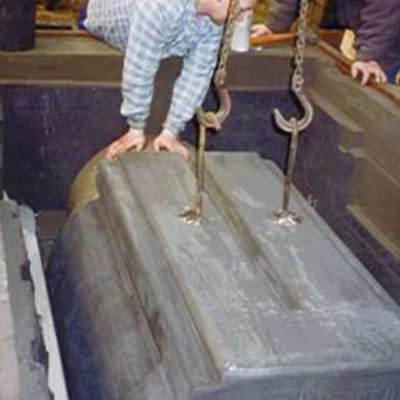
Core is lowered into the mould
One of our larger moulds, a gate valve casting for the water industry. The bits by his feet are the strengthening ribs of the casting. The circular parts either side of the moulder will be cored out and form flanges where the pipes will be attached either side of the valve. The shut off blade will travel from where his right hand is and block the flow between the two pipe flanges. When the core is placed in the mould it will leave a wall thickness of 40 mm for the metal to flow into.
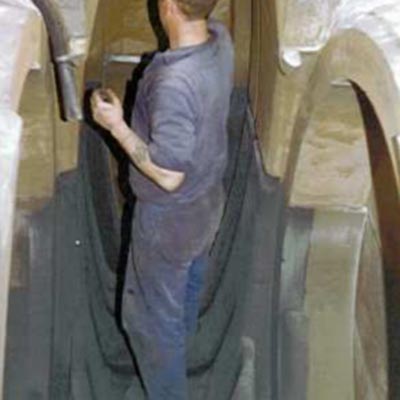
Gate valve casting for the water industry
The foundry produces many of its own patterns for moulding
Non-Magnetic Stator End Plate. One of a pair of 4 tonne castings destined for a power station in Canada.
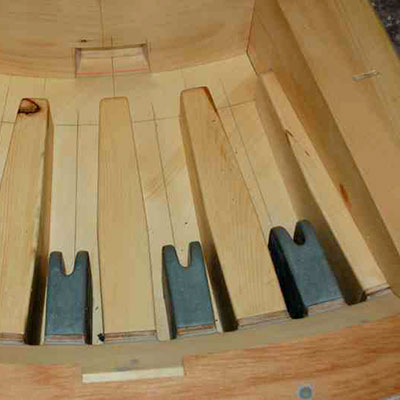
Pattern for Core box
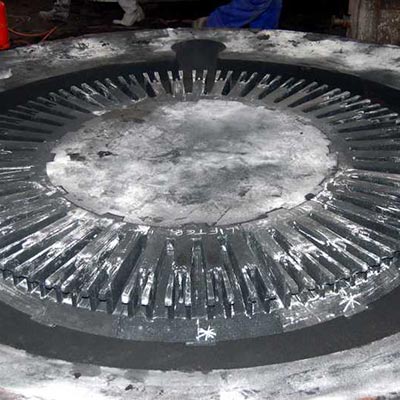
Sand and oil Cores arranged within mould
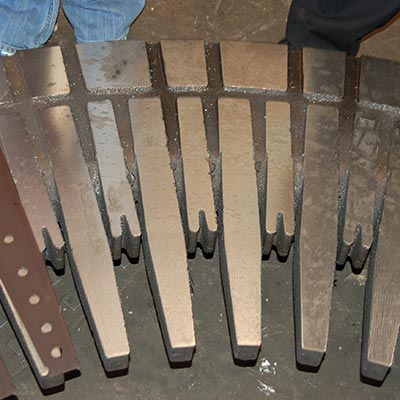
Description